Delhi-based label specialist Kwality Offset Printers has benefited from the Kodak Flexcel NX digital flexo platemaking system. The Flexcel NX technology has helped the company grow in the label printing segment, stated Krish Chhatwal, partner at Kwality Offset Printers in a webinar organized by Miraclon on 6 October 2021. Miraclon is the name of the global company that sells and services the Kodak Flexcel NX technology.
Chhatwal said that Flexcel NX system has helped the company achieve offset-like quality from flexo printing. “We have managed to shift a lot of jobs from offset to flexo. Also, our customers are very happy. When it comes to Flexcel NX, there is very little image correction at the pre-press stage. We end up saving a lot of time and resources,” he said.
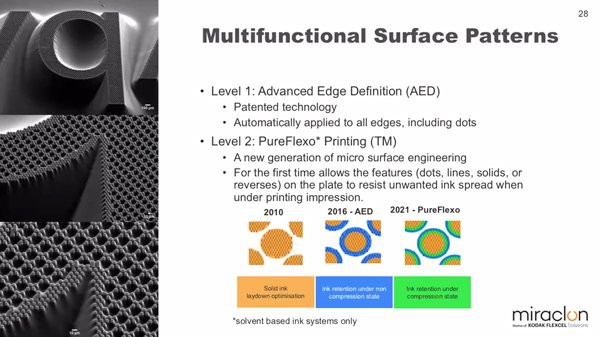
Image PSA screenshot of Miraclon webinar
Case for in-house plate making system
Chhatwal added that even the chemicals used to process the NX plates are cleaner and environmentally friendly. Other salient features of the Flexcel technology are its patented flat top dots with DIGICAP NX patterning which give crisp image production, with good solids and shadow areas and fine highlights – a good tonal range that can be maintained with consistency throughout the print run. “Apart from all this, we get best in class after sales service,” Chhatwal said.
Kwality Offset Printers has been offering label printing solution to leading companies for around 50 years. As one of the leading labels specialists of India, it works for FMCG companies including liquor, food, and healthcare. It also works for leading brand owners in the cosmetic and pharmaceutical industries. Its customers include Pernod Ricard, Nestle, Radico Khaitan, Healthkart, Dabur, Heinz, Perfetti, and Cargill.
The company uses all types of print technologies on its digital, offset, and flexo presses. It has a fully automated production line controlled by a company-wide ERP system.
“We are not just printers but solution providers. We encourage brand owners to talk to us about their projects and plans. By doing this we advise the client about the materials and finishes they should go for. We have always believed in the best technologies and the best materials,” Chhatwal said.
During his presentation, Chhatwal also made a case for having an in-house plate making system and said that this offers multiple advantages. He said that with Flexcel NX in-house plate making capabilities, Kwality Offset Printers has been able to reduce press downtime and offer fast and accurate imaging. He said that with the plate making system, the company has been able to have a complete control over inks and plates. “We have been able to match existing jobs in one go and also been able to save costs on the press with Flexcel NX,” he added.
“We have been able to work seamlessly which has a positive impact on profitability,” he said. “Also, we do not have to rely on third party vendors, which means we can ensure safety of data and artwork that is provided by the customers.”
Vinay Nalawade of Parakh speaks on CI Flexo

Vinay Nalawade of Parakh Flexipack also took part in the webinar to share his experience as one of the earliest Kodak Flexcel NX users in the country for its wide web CI flexo presses for flexible packaging. Parakh’s plant includes blown film lines and several CI flexo presses and also most recently it installed a Bobst gravure line which tends to make Nalawade quite expert on the relative advantages of both processes. Nalawade made clear that using the Flexcel NX system his company was able to compete with gravure for most if not all types of flexible packaging and to leverage many of the advantages of flexography.

Asked to speak about the relative merits of each process in the question and answer session, he suggested that while his company installed four CI flexo presses before installing its first gravure press, there are packaging designs and length of runs that do require gravure. Nevertheless in this webinar he emphasized that Parakh has benefitted from its pioneering work in flexography for flexible packaging in India by being at the leading edge of technology such as the Flexcel system and more recently from its installation of an automated ink mixing plant.
This article has been modified twice, on 14 and 17 October, with additional content and images. – Editor