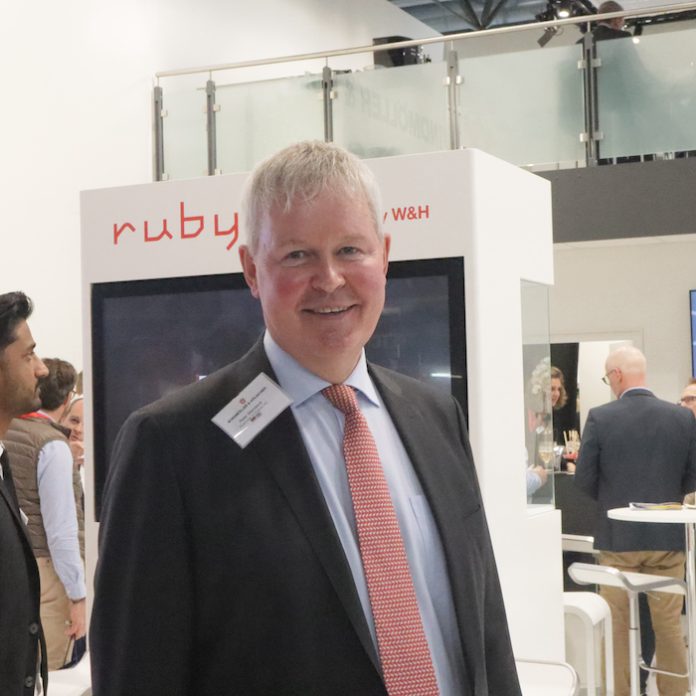
Windmöller & Hölscher presented new machine technologies and packaging solutions for sustainable flexible packaging production at Interpack 2023 in May. The company draws a positive balance from the event, saying, “The change in the packaging industry increases the demand for innovative machines. This offers market opportunities for the technology leader W&H. Sustainability was the biggest driver at Interpack, combined with digitalization and the continuing drive for efficiency.”
Windmöller & Hölscher showed its new de-inkable, recyclable mono-material PE pouch with barrier properties at the Interpack – developed in partnership with ExxonMobil, Henkel, Siegwerk, and Kraus Folie. The films used for these pouches were manufactured using the W&H Varex II extrusion line with an inline MDO and the de-inking primer, and the print image and barrier coating applied by W&H’s Miraflex II CI flexo printing press with the downstream process.
Such products have excellent barrier properties and improved mechanical properties in comparison to multi-material alternatives. It can be delaminated and de-inked allowing for a nearly colorless recyclate which can be recycled very easily, something that was a big challenge with multi-layer packaging.
Additionally, their recent products include the EVOH co-extruded pet food bag and barrier-coated pet food bags, demonstrating a circular economy film concept. These products are designed for recyclability, highest efficiency, and packaging performance, in partnership with DOW, B&B, Siegwerk, and Henkel.
The co-extruded PE-based sealing film (cat food pouch) containing a thin layer of EVOH was laminated with MDO (Machine Direction Oriented) film manufactured on a W&H Varex II and printed on its Heliostar II rotogravure press, producing a sustainable and recyclable PET-free packaging solution.
For the barrier coating bag (dog food pouch), the MDO film was reverse printed and then coated with a PVOH barrier on a Miraflex II CI flexo press with in-line technology in just one go. The film is then laminated to a PE sealing film.
A recyclable high-barrier stand-up coffee pouch is another approach to conquering the challenges of sustainability in the demanding field of high-barrier functionality. With stretched MDO PE film containing an EVOH barrier in combination with an all-PE sealing layer, Windmöller & Hölscher, and its partners created a laminate with only 2% EVOH that exceeds current recycling regulations while maintaining the properties currently achieved by metalized BOPP/PE or BOPET/PE laminate which is non-recyclable.
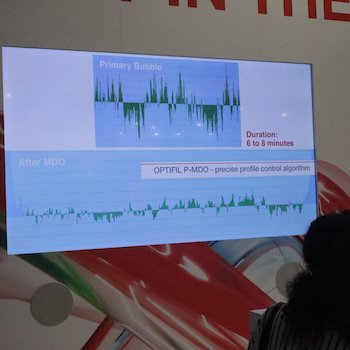
Photo PSA
The latest developments around the company’s IoT platform called Ruby are also something that was highlighted during the Interpack. Ruby offers a platform with various freely combinable extensions to provide a tailored range of functions. It enables continuous monitoring of data in real-time and analysis of production parameters, collects data for future production optimization, remote quality monitoring, and processing of defect detection data.
The mobile app launched at K 2022 in October, makes it even more accessible and easy for W&H customers anywhere to keep an eye on the overall production processes. The Ruby Go and Ruby Check for extrusion and printing respectively, provide complete traceability of inspection data, automated localization of printing defects in downstream processes, and remote quality assessment from the office.
W&H India team contributes to software development
When we visited the Windmöller & Hölscher stand in Hall 12, the Indian team was mostly busy with customer visits to Lengerich or meetings at the top of the stand. This is generally a good sign with the implication of detailed technical discussions and maturing projects.
However, when we revisited W&H on our last day at the show, we briefly met and chatted with Peter Steinbeck, the managing partner of the company. We asked Steinbeck about the progress of the company’s software development in India, a subject that we first brought up at the PlastIndia event in Gandhinagar more than five years ago and which he seemed enthusiastic about. Since then, the overall engineering team in India has more than tripled and we expect that a considerable part of this could be in software.
Steinbeck was quick to answer, saying that the software development work in India is going extremely well for many of the back-office operations of the company. When we asked if this team was also contributing to some of the automation and Industry 4.0 projects, he replied in the affirmative, saying, “Yes, they are involved in these also. The communication between our teams has evolved and is strong now. We are very happy with the developments with the software team in India, and we are on the same page, despite the physical distances.”