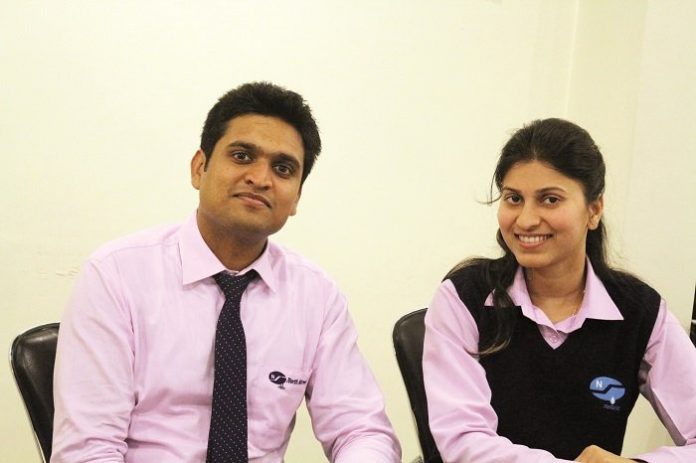
Carbon fiber possesses striking features such as, high strength to weight ratio, corrosion resistance, electrical conductivity, high thermal conductivity and high tensile strength among others. Delhi-NCR-based designer and manufacturer of carbon fiber components, Carbon Light manufactures carbon fiber composite rollers for the packaging, paper and film, mining, printing, rubber, food and other industries. Carbon fiber rollers have been long-used in a number of converting applications as the lower weight and inertia of the rollers support faster web speeds and reduce vibration.
Carbon fiber is twice as stiff and has lower density than steel. Metal rollers need to be powered and controlled by complex electronic systems to avoid stretch and damage on films but the lightness of carbon fiber allows the use of fewer motors, electronic drives and control systems. Used by a number of customers in India as well as foreign countries, Carbon Light has been involved in manufacturing carbon fiber rollers for the last five years and doesn’t plan to manufacture metallic rollers at all, even though 95% of the market is dominated by metallic rollers. “We aren’t going by just current demand but have entered this segment forecasting future demand. Any change takes time to incorporate in the overall system. Now, with the films and material being processed, aluminium is the most suitable material as it is more economical and has a service life of around 3-4 years. But, for wider formats of 2.7 or 3 meters, aluminium or steel no longer remain an option, one has to go for carbon fiber. All international OEMs for the past 25 years have been using carbon fiber rollers and have set it as a standard,” says Anuj Bansal, technical manager of Carbon Light.
“There are companies in India who are our customers such as Uflex which manufactures films up to 10.5 meters wide. Even though this technology is not in common use in India, key players such as Uflex and some other companies have been using carbon fiber rollers in their machines as a standard. For these OEM’s, we act as a key supplier of rollers,” says Rini Bansal, business development manager of Carbon Light.
In India, there is no other company at this point, which manufactures carbon fiber rollers. Right now, CL is providing carbon fiber rollers at the most pocket-friendly rates. All other carbon fiber roller manufacturers are currently located in Europe and their costs are higher in comparison to Carbon Light.
The company first found demand for carbon fiber rollers in printing. Initially it was manufacturing drive shafts for cooling towers. A few print customers, approached CL advising them to manufacture carbon fiber rollers since they are based on a similar manufacturing technology. The printers were not finding any carbon fiber roller manufacturers locally and were being forced to squander money on imports.
In order to grow their customer-base, the company is educating potential customers. CL plans to add and develop new coatings for its rollers to tackle new substrates under development and improve their viability.
In overseas markets, the company sells rollers to end-users. “Supplying to the OEMs will be a big challenge although we’re working on that right now. Since, the European market is not easily open to new suppliers, it is difficult to penetrate there. The big players in Europe never compromise on quality or look at options, they just go with the established suppliers in their region,” Anuj Bansal added.
Flexo sleeves
CL also started manufacturing flexo sleeves for flexographic printing less than a year ago. “The exact formulation and the taper that the sleeve has is very critical. So, we have bought some new blending machines which can give us precision needed to deliver exact dimensions as well as flexibility and rigidity required for individual sleeves. Thus, we have many existing roller manufacturers approaching us just for the sleeves and they can possibly do post-processing and reach out to the market,” Bansal concluded.