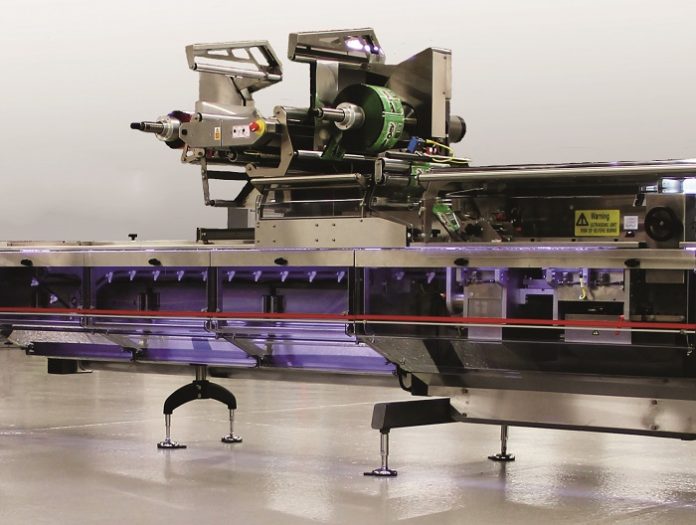
Pack Expo Las Vegas has steadily grown into one of the largest processing and packaging events in USA — an event known for showcasing the innovation of top-tier suppliers. It’s where corporate- and plant-level managers, engineers, production professionals, brand managers and package designers can connect with suppliers, talk shop and gain perspective on the industry.
Pack Expo Las Vegas 2015 and the co-located Pharma Expo 2015, a joint venture from PMMI and the International Society for Pharmaceutical Engineering (ISPE), have over 800,000 net square feet of combined exhibit space. They are expected to attract 30,000 processing and packaging professionals and more than 2,000 exhibiting companies. Registration is US$ 30 through 14 September, when it increases to US$ 100. Register for Pack Expo and Pharma Expo at packexpolasvegas.com.
Lenze Americas will sponsor the PMMI member and exhibitor lounges at Pack Expo and the co-located Pharma Expo show, according to show owner and producer PMMI, The Associat- ion for Packaging and Processing Technologies. “The PMMI member and exhibitor lounges at Pack Expo and Pharma Expo are essential show features, allowing the personnel staffing booths to take a break from the busy show floor,” said Charles D Yuska, president and CEO, PMMI.
Bosch’s two-in-one biscuit packing system Stand C2800

Following a highly successful field test with United Biscuits a leading international biscuits and cakes manufacturer, Bosch Packaging Technology will for the first time showcase its innovative two-in-one biscuit packaging system at Pack Expo LasVegas 2015. Launched at interpack 2014, it is the first system of its kind capable of pack style changeovers from slug to pile packs in less than three minutes, offering flexibility to biscuit manufacturers.
With state-of-the-art product handling, horizontal flow wrapping and secondary packaging equipment, the system is designed for gentle and versatile wrapping and case packing of even the most delicate biscuit products. A customized field test at United Biscuits in Manch ester, UK, effectively handled the primary and secondary packaging of the manufacturer’s McVitie’s Jaffa Cakes brand in different formats and sizes.
The two-in-one biscuit packaging system achieve shigh-speed, fully reproducible change overs by using the same feeding components for both pile and slug packs, increasing productivity and uptime. It is the only system of its kind capable of changing the pile configurations in record time. No matterif 1, 2, 3, 4, 5 or more biscuits are required, pile packages with a maximum height of 50 millimetres (about two inches) are possible.
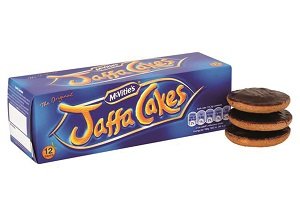
a single line during a recent successful field test
“We developed the two-in-one biscuit packaging system as our response to a growing retailer and consumer demand for flexible packaging formats, like smaller on-the-go and larger family packages,” said Daniel Bossel, product manager at Bosch Packaging Technology.
Agentlehandling philosophy across the line ensuresminimized damagehazards and product contact, making the two-in-one biscuit packaging system suitable for even the most fragile, brittle products. Additionally, three-dimensional product inspection technology detects broken biscuits and sorts them out. The hygienic designprevents thebuild-upof crumbs andallows for easy cleaning,facilitatinga continuous production and maximized uptime. As part of Bosch’s Seamless Systems portfolio, the speeds of all line components are balanced to eliminate bottlenecks and optimize production flow, from distribution to secondary packaging. The integrated design concept with the same look and feel across the entire line with standard operating proceduresmakes the entire systemas simple to operate as a single
machine,reducing the risk of operator errors.
Complementing primary packaging, the biscuit system is designed for a wide range of case packaging formats for RSC or HSC cases (Regular and Half Slotted Containers) with retail-ready functionality. The case erecting, robotic loading and optional case closing units are all integrated in the case packer, resulting in a reduced footprint.
Bradman Lake’s FT120 flow wrapper Stand C5003
Bradman Lake Group is participating at the Pack Expo LasVegas show that will be held from 28 to 30 September 2015 at the Las Vegas Convention Center where visitors to Bradman Lake’s Stand C-5003 can see the latest technology in horizontal flow wrapping and cartoning equipment. Bradman Lake will be exhibiting the FT120 flow wrapper with SPF shuttle phase feeder and the RA90 three-flap top load carton closer. These machines combine over 65 years of experience designing and building packaging equipment and installing more than 15,000 machines worldwide.
The FT120 sets the benchmark for horizontal form fill and seal flow wrapping machines and the SPF is an innovative, non-back pressure feeder for the most challenging of product types. The RA90 right angle flexible carton control, lugless, three-flap cartonlid closeris designed tohandle a variety of chip andmicroflute corrugated boards and the version to be demonstrated includes the new servo motor driven lift and descend feature which controls the overhead conveyors. This replaces the earlier cantilevered design and provides excellent operator access from all sides of the machine and facilitates rapid size changeover.
Brenton’s robotic palletizing system Stand C3121

At Pack Expo 2015, Currie by Brenton, powered by Pro Mach, will showcase a small footprint robotic palletizing system for automated pharmaceutical applications. This Currie by Brenton design reduces by up to 40%, the floor space typically required by robotic palletizers. The robotic palletizeris part of an active demonstrationof a fully automated and unifiedcasepacking,palletizing, andstretchwrapping operation.
As cases exit the Brenton Mach-2 wrap-around case packer each is checkweighed before being handled by the robot. An incorrectly weighted case is automatically picked up by the robot using the vacuum pick tool and placed on a reject lane. Every in-specification case is picked up by the robot, which then moves the case to a labeller and then to a vision system. Similarto a vision station in the case packer, this vision system verifies that the barcode andhumanreadable information on the label are correct.
The unified system’s end-to-end quality control features are basic to tracking and tracing pharmaceutical products. The control panel for the case packer and robot has been consolidated into one compact unit and mounted directly to the frame of the case packer for additional space savings.
The HMI for the case packer and the robot have been integrated for unified operation and utmost ease- of-use. Control of the robot is carried out through the HMI, a much simpler and more intuitive process than programming movement through a teach pendant.
Another space savings aspect is that the robot builds pallet loads directly on the base of an Orion Packaging FA turntable automatic stretch wrapper. This stretch wrapper features Orion Packaging’s (Stand C-3023) latest control system with enhanced HMI, which is being introduced at Pack Expo. The high resolution imaging on the HMI makes diagnosing problems with wrapped pallets and maintenance on the unit easier than in the past.
Marchesini’s Compact 24 Synchro Stand N635
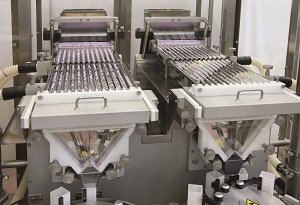
The Marchesini Group will be presenting a new counting line for the American market. Compact 24 Synchro is a monoblock, which is able to run high production speeds combined with top counting precision. This monoblock will be showcased at the trade show with the Sirio 3 bottle unscrambler or bottom code reader. The Sirio 3 is capable of handling round, square, oval orrectangular containers.
Compact 24 Synchro is one of the latest packaging innovations by Marchesini Group forthe solid dosage packaging market. This monoblock is designed to manage high production rates (up to 150 vials a minute), at the same time ensuring the highest possible counting precision. The combination of counting accuracy at high speeds is due to the combined use of two technological innovations by the company’s R&D department.
The first is a so-called Twin Flap technology that increases the speed of the 12 channels of each counting unit by drastically reducing the dwell time of the bottle under the funnel, without increasing the number of contact parts. The second innovation is the Synchro-dynamic conveyance system that transfers the counted product into the vial in continuous motion as the vial itself is fed along the line.
The Synchro-dynamic process along with the Twin Flap technology, which splits the 12 channels of each counting unit into two, thus creating a double counter for each unit, ensure the most reliable and accurate counting technology available. The final result is the most innovative monoblock solid dosage counting line on the market today, which guarantees complete efficiency of the production process – from the upstream phase of counting to the insertion of the cotton, right through to capping.
Marchesini Group will be exhibiting in Pack Expo 2015 after Cosmopack 2015 (which will be held in New York from 16 to 17 September), the biggest international trade fair dedicated to various applications, components and solutions for the production of cosmetics.
Plexpack’s Emplex MPS 7103 Stand C4600
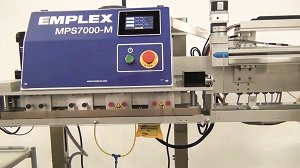
Plexpack delivers flexible packaging machinery solutions for customers worldwide. The company’s Emplex bag and pouch sealing and Damark shrinkwrap and bundling systems are customizable, made-to-order with your unique needs, reputation and budget in mind. Modular and innovative designs are easy to install, maintain, and expand. They provide line and product flexibility, and ensure your packaging operations perform to the highest standards.
At Pack Expo Las Vegas 2015, which will be held from 28 to 30 September, Plexpack will be featuring at Stand C-4600 the latest solutions for continuous vacuum sealing, print, scan or reject systems and others technologies. The Emplex MPS 7103 is ahigh-speed, continuous band sealer equipped with a vacuum and nitrogen gas flush system for creating high quality moisture proof, oxygen free packages. Typically, customers requiring more than 15 bags a minute find a greater return on investment by choosing a continuous band vacuum sealer. Customers include producers of coffee, snacks, pre-baked goods, electronics, medical products, and fresh or dried food, produce and meat.
The MPS7103 can operate as a standalone sealer or be paired with a synchronized conveyor for a more automated system. Bags less than 2 lbs. are easily sealed without a conveyor. The MPS7103 provides high quality, hermetic seals on all moisture barrier bag materials and is capable of sealing bags up to 12 ml in thickness or 6 ml maximum when gusseted at required production speeds.
The vacuum and nitrogen gas flush system removes more than97% of oxygen and creates a moisture-free package, resulting in longer shelf-life, product integrity, and protection against discoloration. For snack products a gas flush only system can create a cushion-like buffer against damage.