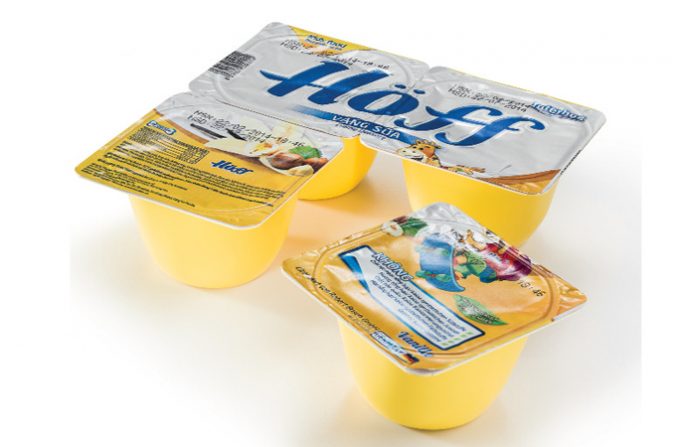
Founded in 2012, Interbos is one of the leading dairy producers in Vietnam. The company’s main plant in Hung Yen, near Hanoi, is specialized in premium dairy products, including creme desserts, fresh cheese and nutritious yoghurts. To provide the highest product quality possible, the company raises its own cattle and produces its own milk on several company-operated farms. Interbos also helps local farmers by sharing best practices for feeding, correct nutrition and sustainable farming, and offers financial aid for microfarming.
A new chapter
Inline with Interbos’ philosophy of delivering premium products to its customers, the company set its sights on breaking the mould for the traditional yoghurt packaging in the country. With the new aseptic filling and safe packaging the risk of quality loss and spoilage can now be avoided, especially during transport and storage without sufficient cooling. The production line consequently would need to allow Interbos to develop a formula that does not use artificial flavours or preservatives and still extend the product’s shelf-life for a minimum of six months outside of the cold chain. It also needed to ensure the desserts and yoghurts would be protected from the country’s warm summers, especially when the temperature exceeded 45 degrees Centigrade with high humidity.
The quest for quality
After considering several suppliers, Interbos selected a well known global brand – Bosch Packaging Technology for the project. Bosch focussed on developing a versatile solution that would allow production of the desired product formula while maximizing product safety and keeping costs in check. The end result was a production line centered around Bosch’s TFA 4818 aseptic thermoform, fill and seal machine which features a fully enclosed tunnel, eliminating the need to invest in a clean room environment and did not require a large footprint.
The machine allows the aseptic packaging of commercially sterile products for ambient temperature storage without the need for preservatives, retort processing or refrigeration. Consistently high product quality that meets FDA and VDMA standards is provided through high-precision cup wall-forming and the fully enclosed aseptic tunnel with continuous monitoring for over-pressurized sterile air.
To help prevent operator errors that could lead to contamination issues, Bosch integrated two precise, full-metal piston fillers capable of running maintenance-free for the first year. Ease of operation was also ensured through low overall maintenance requirements and an intuitive HMI in Vietnamese. In addition, roll stock materials minimize storage space, ensuring cost-effective packaging and handling.
The start of a journey
“Withthe first aseptic thermoform,fill andsealmachine inVietnam,we are able to provide high quality,fresh products with long shelf-life on a single production line,” says Tuan Khai, founder and general director at Interbos. ”
“The new machine has delivered everything we had hoped for – the product is well received by our customers and even other dairy producers were amazed with the product and its high quality. But our journey has just begun. Now that we have a line capable of delivering to FDA and VDMA standards, we have the opportunity to produce much-needed new products, such as baby food, here in Vietnam in the future,” concludes Khai.