If one of the mega-shows in the West keeps growing, it’s K, the Plastics, Resins and Rubber show at Düsseldorf Messe. K stands for Kunststoffe, German for Synthetics, and its exhibits consist of machinery and materials for the four largest plastics user industries: packaging, construction, automotive and electronics. Whereas the latter three of these are interested mainly in lightweight composites, 3D printing and design, members of the packaging industry visit this show for the large array of compounding, pelletizing and extrusion lines, the molding, compression, foaming, casting, pultrusion and thermoforming equipment, as well as in-mold labeling, object printing, flexible packaging printing and converting machinery, and all kinds of ancillary devices. Most of the larger exhibitors have running machinery both at their booths and at Open House demonstrations at their manufacturing plants, some of which are nearby. Ron Augustin and Naresh Khanna report on the event.
Held every three years during eight days in October, this year’s event attracted some 230,000 visitors, including almost 30,000 from Asia. While the total number of visitors was up from around 220,000 at previous shows, the Asian numbers were slightly down, mainly due to a steady decrease in visitors from India as reported by the organizers (9,000 as compared to 10,000 at K2013 and 11,000 at K2010). The number of exhibitors from India also was down to 104, from 145 at K2013. Out of the total of 3,285 exhibition stands (a number growing by a few dozens from show to show), 752 were taken by Asian companies, of whom 400 from China and Hong Kong, 127 from Taiwan, 46 from Korea, 30 from Japan, 17 from Malaysia and 28 from Thailand, Vietnam, Singapore, Indonesia, Pakistan, Australia and New Zealand.
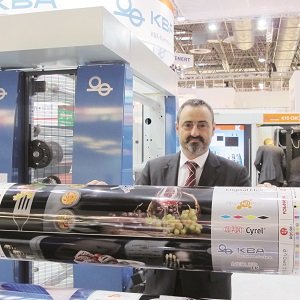
flexotecnica S.p.A. Photo PSA
Extrusion lines for blown film, lamination and coating were shown by more than 80 exhibitors, from the likes of Bobst, KraussMaffei, Reifenhäuser, Windmöller & Hölscher, Baldwin, Bandera, Macchi and Oerlikon to smaller players such as Rajoo Engineers from India and a majority of companies from China, Korea and Taiwan. Extruders for other applications less used in the packaging industry were shown by Bengaluru-based Steer Engineering and a large number of Italian and East Asian companies. Thermoforming machinery used for the production of thin wall yoghurt cups and food containers was taken to the show by Brückner, COMI, OMG, Rajoo Engineers, Rohde, Swiss company WM Thermoforming and over a score of companies from East Asia. Injection molding equipment could be found at the stands of Ilsemann, KraussMaffei, COMI, Ferromatik, Romi and many others. Compounding, grinding, mixing, filling, welding, cutting, slitting/rewinding, wrapping and all sorts of ancillary and processing equipment completed the machinery on show, next to the presentation of new materials and packaging innovations.
In printing and converting machinery, Bobst, Cerutti, Comexi, Kampf, KBA-Flexotecnica, KBA-Kammann, Mimaki, Omso, Polytype, Soma, Tampoprint, Uteco, Van Dam and Windmöller & Hölscher were the big runners once again, accompanied by around fifty smaller manufacturers from Asia, Italy and Turkey. Turkish manufacturers were particularly present in the in-mold labeling machinery section.
Comexi released a new printing unit for its gravure press R2 and showcased its latest offset press C18 launched at drupa earlier this year. Comexi also had its L20000 water-based laminating machine on show, next to new coating solutions and its S1DT slitter/rewinder. Czech company Soma showcased its successful Optima 2 flexo press launched at drupa 2016. Gallus had a small stand together with Sun Chemical, showcasing the Gallus Screeny G-Line for screen printing on glass and containers.
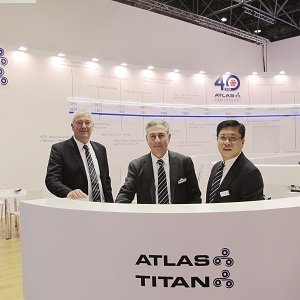
manager, Peter Barnes and Raymond Chan, regional
sales managers at Atlas Titan. Photo PSA
Proven and new film grades and barrier materials for flexible packaging could be found at nearly 200 booths. LyondellBasell, for instance, presented a range of easy-peel polybutile film, non-phtalatate polypropylene based film and polypropylene grades for transparent cups. Control and automation devices could be found at the stands of Bosch-Rexroth, BST eltromat, Bühler, Robomaxi and X-Rite, to mention just a few.
Reifenhäuser’s managing director Ulrich Reifenhäuser, chairman of K’s Exhibitor’s Council and head of the plastics processing machinery group at German trade association VDMA, took a bet on the results of K 2016, “Never before did I sign so many orders at our K stand as this time. I would bet this K to have been the best ever.”
Arvind Rub Controls
The Ahmedabad headquartered manufacturer and exporter was promoting its rubber rollers and sleeves for flexo and gravure presses and film laminators. Interestingly, Arvind Rub Controls showed samples of flexo sleeves for direct laser engraving plates for wide-web flexo CI presses that it plans to manufacture. Also represented at the stand was Ahmedabad-based Image Gravure, a company that exports electronically engraved gravure cylinders.
Atlas Titan
Philip Nichols, marketing and communications manager at Atlas Titan, said at K that the company is enjoying its best sales year ever although the slitter rewinder market remains highly contested. In South Asia, the company is especially successful in the primary rewinder slitter market as large investments in film lines continue apace at companies such as Jindal Polymer.
In the secondary slitter rewinder market, the company’s SR 800 launched in 2015 has become a hugely successful product. It has filled the void between the entry-level and the high-speed SR9DT turret machines with autosplicers running at speeds as high as 1,000 m a minute. Atlas Titan’s success in the competitive market is credited firstly to the precise tension control of its rewinders in addition to their quality and reliability in production.
Bobst K5 metallizer for transparent film coatings

Tech, Anant Patel, partner at Image Gravures and
Jitendra Patel, CEO at Gayatri Rub Tech. Photo PSA
At its K stand, Bobst showcased its full range of flexible packaging samples printed on its range of gravure and flexo presses. Highlighted were samples of metallized films produced on the company’s new K5 Expert metallizer. The K5 mettalizer was actually launched on 18 October, the day before K started, at an Open House at the Bobst Competence Center in Manchester, UK.
The alubond process is a breakthrough in metal adhesion technology wherein the aluminum oxide sprayed onto the film in the vacuum metallizer turns into a thin ceramic layer which is transparent. Likely to be of great interest to the Indian and South Asian flexible packaging industry, the ALOx metallizer produces a printable film where transparent areas can show the product inside. Another feature is that the strongly bonded ALOx ceramic layer and the base film cannot be peeled apart.
Brückner
Brückner’s main business consists of film stretching lines. The demand for these lines in North America and Western Europe seems stagnant. In the first half of 2016, the majority of the orders came from Asia with China (35%), India (19%) and South Korea (15%), Taiwan (10%) representing more than three quarters of its film line sales so far. The family-owned company has however diversified rapidly in the past three years with several acquisitions through its Keifel thermoforming and PackSys Global packaging tube machinery subsidiaries.
E+L’s Ultra-HD image monitoring, ELTISS, ELTIM inspection
The new print image monitoring system ELSCAN OMS6 contains two 12 megapixel cameras, which ensures exceptional image quality in Ultra-HD (4x HD) with perfect color reproduction, without apparent distortion in the edges of the image. Thanks to the maintenance and wear-free fixed focus lenses, it can be zoomed without delay. The short flash times of the extremely durable LED flash permit web speeds of up to 1200 m a minute. Optionally, special UV and paint flashes can be used to illuminate particularly critical print images perfectly.
E+L’s proven inspection solutions showcased at K included the ELTIM measuring system for the contactless measurement of layer thickness, basis weight and other material properties using ultrasound with a measuring accuracy up to 0.2%; the ELSIS for surface inspection with the OL 60 line scan camera, whose image processing functions have been continuously further developed for the detection and classification of complex and low-contrast defects. Every E+L camera is an independent image processing system that communicates with the ELSIS server and the other cameras in the system via Ethernet making the inspection lines very compact and easy to integrate quickly.
Gayatri Rub Tech
Gayatri had a successful K exhibition with strong sales and feedback from its traditional export clients as well as new enquiries for its rubber rollers and sleeves. These are widely used in gravure and flexo presses and in solvent and solvent-less laminators, often as OEM components for leading equipment manufacturers, especially gravure press manufacturers based in India.
The Ahmedabad-based company has been exporting its products since 2005, and one of the new products highlighted at its K stand were direct laser engraving flexo sleeves for wide web CI flexo presses. As direct laser flexo sleeves become increasingly viable, one can expect a jump in wide web flexo presses being installed around the world and especially in Asia. Gayatri is looking to grow its exports from the current level of approximately one-third of production. It has recently invested in a second plant in Gujarat to accommodate manufacturing equipment sourced from Europe.
KraussMaffei
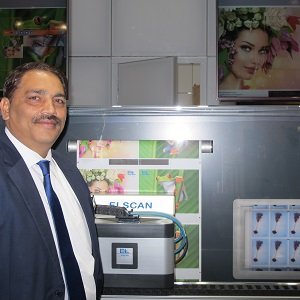
cameras can move at positioning speeds of up to
900 mm a second. The drive unit is collector-free,
making the camera crossbeam virtually wear free.
Web widths of up to 2800 mm can be implemented.
Photo PSA
KraussMaffei launched its modular and all-electric PX injection molding machine by showcasing five customized PX versions for applications in the medical sector, electrical engineering and packaging. Other KraussMaffei launches included its Thermoplastic Resin Transfer Molding system particularly geared at the automotive industry. It also presented its APC plus system for thin-wall and cascade injection molding developed two years ago as well as its full range of equipment for the thermoforming and over-molding of organic sheets, injection molding coating and finishing machines.
Rajoo Engineers’ energy-efficient 5-layer blown film line
Rajoo Engineers demonstrated 5-layer all PE film production at its stand at K. With a large footprint of installations in India and increasingly in North and South America, Africa and the Far East, the company now has global high technology partners including Alpine and Bausano. The company is vying for a leadership position with its affordable technology while pioneering advanced solutions that are energy efficient and ready for Industry 4.0. Sunil Jain, president at Rajoo Engineers stated, “We have the most energy efficient blown film line at K.”
Reifenhäuser
Reifenhäuser showcased new developments in its blown film extrusion, cast film extrusion and thermoforming sheet extrusion lines. Its Evo 5-layer blown film line was shown with an inline stretching system allowing for 50% thinner film extrusion. The company also showed its new Evo Ultra Die 9 barrier die heads, Evo Ultra Cool FFS cooling system and Evo Ultra Flat film flattening unit. In cast film and sheet extruding, Reifenhäuser presented a Midex 9-layer cast film extrusion line with co-extrusion feedblock for better layer distribution, a Midex-RA rotary arm for multi-web winding, a Mirex-MT-V-AX polishing stack with gap adjustment, and a Mirex Monolayer thermoforming sheet line combined with an ILLIG thermoformer for conical cups.
Windmöller & Hölscher
Windmöller & Hölscher unveiled three novelties at K2016: the Filmex cast film line with film performance monitor FPM, the Varex blown film line with Turboclean resin purging system, and the Optimex blown film line. The Filmex II shown at the nearby W+H plant in Lengerich is designed for stretch, CPP and barrier films and demonstrations included the production of 13-layer barrier film of which the consistent quality was maintained by data fed from the FPM performance monitor.
On the 5-layer Varex II shown at Lengerich, 48 gsm film stretched to 12 gsm also increased the breathability of the film which is desirable for the fast growing hygiene industry. Additionally, the automatic changeover between different resins using the Turboclean module was shown. The Optimex designed to produce a broad range of 3- and 5-layer high quality films at an attractive price was shown producing films for standup pouches at K. At Lengerich, amongst the ten film lines and presses, the new Dynastar narrow web short run gravure press was also demonstrated in an 8-unit configuration.