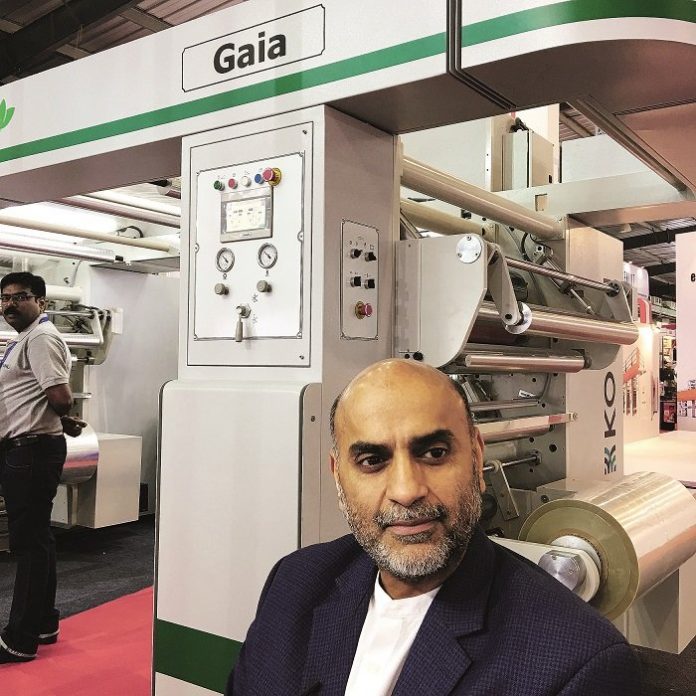
The Plastindia exhibition in Gandhinagar from 7 to 11 February 2018 showed the strength of the Indian and South Asian packaging industry, and particularly its flexible packaging
segment. A standout aspect of this show was the remarkable mix of leading global manufacturers and a high number of Indian manufacturers of masterbatches, films, rollers, extruders and dies and printing, converting and filling and sealing equipment. There were also many manufacturers of equipment that are needed to turn plastic waste into small pellets and fine plastic powder in order to make various recycled products.
As far as gravure printing machines, the leading Indian manufacturers such as Kohli, Pelican and Expert are already well known for their newer and faster automated presses. Indian-made laminators were also one of the highlights of the show, including the new SP
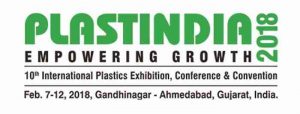
Ultraflex Roboslit Plus slitter rewinder running at 1,000 meters a minute—reliably claimed to be the fastest flexible packaging machine manufactured in India. What was exciting about the new Roboslit plus running at 1000 meters a minute was the smooth acceleration
to full speed accompanied by the quiet whining sound emanating from the evacuating fan that sounds like a wellinsulated mini jet engine. Needless to say, the slit and rewound reels were perfectly neat and clean.
Indian customers for gravure and flexo presses and converting equipment including laminators are increasingly looking at more sophisticated machines, such as the new Uflex coextrusion twin laminator also shown in Gandhinagar, and at higher quality,faster speeds and quicker job changes—all of which point to greater automation and ease of changeovers as well as the use of better film substrates and inks so that the entire system is productive as well as compliant with increased regulations for safety, health and the environment.
Technical and marketing collaborations
A new feature of the Indian manufacturers is collaboration with each other and often with leading international consultants and technology partners. We met some of the players in the Multigraph Machinery group, including its president Hiten Mehta, who is also the owner of Perfect Printgraph, and Kaku Kohli of Kohli Industries, who manufactures both gravure presses and laminators, and later with the top management of Manugraph. This is a joint marketing project in which Multigraph group offers a range of Indian manufactured equipment to domestic and global customers. From narrow web label flexo presses to wide web gravure and flexo presses and laminators, there is a common sales organization for most markets.
At the joint Multigraph stand, Perfect Printgraph showed an electronic line shaft (ELS) stack flexo press with high quality registration while Kohli Industries showed its solvent-free Gaia laminator capable of running at 450 meters a minute. Manugraph was also at the shared Multigraph stand with its Italian technical collaborator Comiflex highlighting the gradual manufacturing program for its gear-less CI flexo press. The first press—a CKD installation—is already being installed at a flexible packaging printer in North India. The Multigraph marketing combine has been exporting Multitec’s narrow web label presses and has also sold a good number of Kohli Industries’ gravure presses to the domestic market while Kohli has itself exported perhaps a slightly higher number.
Jayesh Pathare of Exzone Solutions, who sells green technologies for flexible packaging, showed us the Honeywell System for measuring the solvent content of the air being evacuated from the dryers of the Perfect Printgraph ELS stack flexo press. This system can help improve the efficiency of the solvent recovery system, which is going to become essential for flexible packaging presses as they meet with plant audits by brand owners and government regulations.
Made in India CI flexo presses
It’s clear that while flexible packaging in India is still dominated by gravure and converters are increasingly looking at precision built automated presses above 400 meters a minute,

Solutions with the Honeywell
solvent measuring system attached
to the hot air evacuation system of
the Perfect Printgraph ELS
stack flexo press in Hall 7 at
Plastindia 2018
flexography made an unprecedented showing at Plastindia. Several Indian manufacturers are coming to market with locally manufactured wide web CI flexo presses at a variety of cost, quality and automation levels. With the coming of digitally engraved flexo sleeves, one can look forward to a wider expansion and acceptance of CI flexo printing in India for flexible packaging.
Apart from Manugraph, who has already installed one CI flexo press that it imported, Uflex has begun to conduct live trials of its highly automated Uflexo CI flexo press. Other Indian manufacturers such as Echaar, Ishan International and Innovative Flexotech are also building wide web CI flexo presses. Of these five manufacturers, three are working with Italian technical collaborators and building gear-less presses with a considerable degree of automation.
Global manufacturers are upbeat about Indian developments
Interestingly, the major global manufacturers of flexible packaging presses at Plastindia were actually quite upbeat about the technology improvements of the Indian manufacturers. They seem to think that this will expand the market and allow them to highlight the higher technology features and efficiencies of their own equipment. They are encouraged both by the enhanced technology of locally manufactured equipment and the impending sustainability compliance issues which they hope will extend to operator and plant safety.
The perception is that the induction of automation components and precision manufacturing will eventually enlarge the customer base for higher technology and greater overall efficiencies that go hand in hand. The result should be higher quality plastic-based packaging that is produced efficiently and with sustainability, health and safety coming to the forefront of the overall project and system discussions.