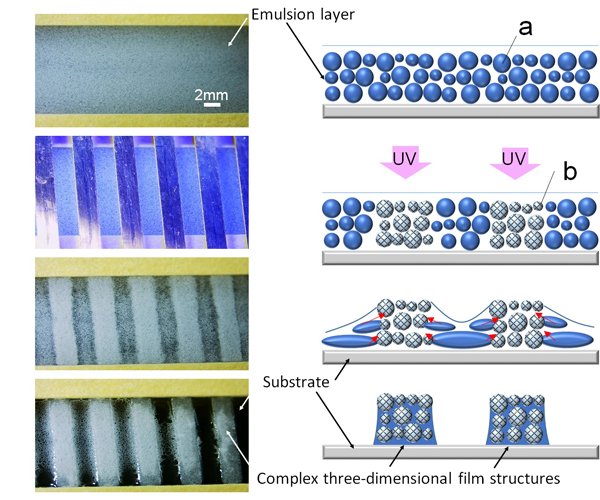
Tokyo – 16 March 2022 – A paper by Toppan researchers on a novel patterning method that utilizes the transformation1 of UV-curable emulsion was published in Springer Nature online journal Scientific Reports2 on March 4. The research establishes the world’s first spontaneous film structure formation technique with low environmental impact establishes in principle with low environmental impact.
The patterning method described in the paper is based on a new principle for creating fine structures by making material spontaneously flow into sections exposed to light. The technique involves no special materials or complicated processes and facilitates the formation of complex three-dimensional film structures with heights in excess of 1 mm. The absence of a development process means that this method produces no waste substances or fluids other than water and has the potential to contribute significantly to the creation of a sustainable society through its application to manufacturing processes for diverse products.
About the research paper
Title: Spontaneous patterning method utilizing transformation of UV curable emulsion
Authors: Yoshimi Inaba, Hideo Asama
Featured in: Scientific Reports (Springer Nature)
URL: https://www.nature.com/articles/s41598-022-07525-5
Background to the research
The formation of fine, three-dimensional film structures, such as surface treatment of electronic components or décor materials, including wallpaper and flooring, entails multiple processes, each of which not only requires significant volumes of various chemicals and cleaning water, but also consumes a large amount of energy. There is therefore a need to simplify the process and develop technologies that reduce consumption of chemicals, water, and other resources, and do not produce waste liquids. To address these issues, Toppan has researched new patterning methods that leverage the material processing technologies it has thus far accumulated.
Overview of the research
1) Establishment of novel patterning method
Toppan has established an original technique called the “emulsion transformation method for patterning” (ET method), which utilizes the transformation of UV-curable emulsion to form complex three-dimensional film structures.
The ET method is the world’s first patterning method to take advantage of the physiochemical behavior of photocurable resin material when mixed with water and emulsified. The material becomes solid due to UV irradiation and the curing reaction in the medium, and patterns are spontaneously formed in the subsequent drying process. This eliminates the need for a development process to remove residues and enables the formation of complex three-dimensional film structures, such as concavo-convex structures with heights exceeding 1 mm.
- Confirmation of principle of continuous patterning in roll-to-roll process
Toppan has confirmed the ET method can be applied to roll-to-roll processes for the continuous formation of a given pattern on a film substrate. When the ET method is used in a roll-to-roll process, patterns can be formed not only by exposure using pattern masks, but also by using a projector for irradiation with patterned light. This makes it possible to switch between various patterns during processing or form continuously changing patterns. In addition to facilitating manufacture of ultra-small lots, including custom-made items, at low cost, this means that cylinders or plates do not need to be changed, enabling leaner, more efficient manufacturing lines where operating time and material loss for substrates and intermediate materials can be reduced.
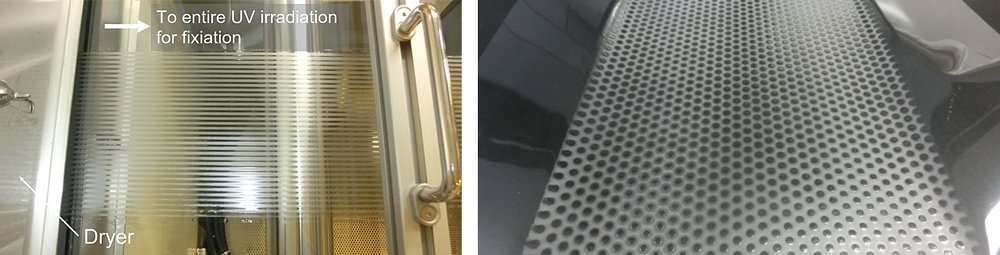
Toppan intends to advance research targeting application to manufacturing processes in a wide range of fields and establish eco-friendly manufacturing methods based on roll-to-roll processes. In particular, Toppan will focus on application to the manufacture of electromagnetic wave suppressing components that use conductive materials and of products with smooth cross-sectional structures, which have been difficult to fabricate with previous methods.
“While conventional patterning methods are predominantly based on chemical reactions, the ET method is a technology based on both a chemical reaction and physical action,” said Yasutaka Kikuchi, Executive Officer and Head of the Toppan Technical Research Institute. “This new technique has many potential advantages for manufacturing and the environment, and Toppan will continue to think outside the box in R&D targeting innovative technologies that contribute to a better society.”
1. Changes in the size and shape of emulsion droplets during the drying process and change from liquid to solid due to change in properties caused by curing of droplets.
2. Scientific Reports is an open access journal publishing original research from across all areas of the natural sciences, psychology, medicine and engineering.
For more information, visit https://www.toppan.com/en/ or follow Toppan on LinkedInhttps://www.linkedin.com/company/toppan/. https://youtu.be/piSuoys5Ii8
Toppan, a global leader in communication, security, packaging, décor materials, and electronics solutions, conducts research on patterning methods used in the manufacture of electronic components and the surface treatment of such products as décor materials. The company has recently also increased its stake and taken ownership of the Max Films business including including its film manufacturing plant in Punjab in India.