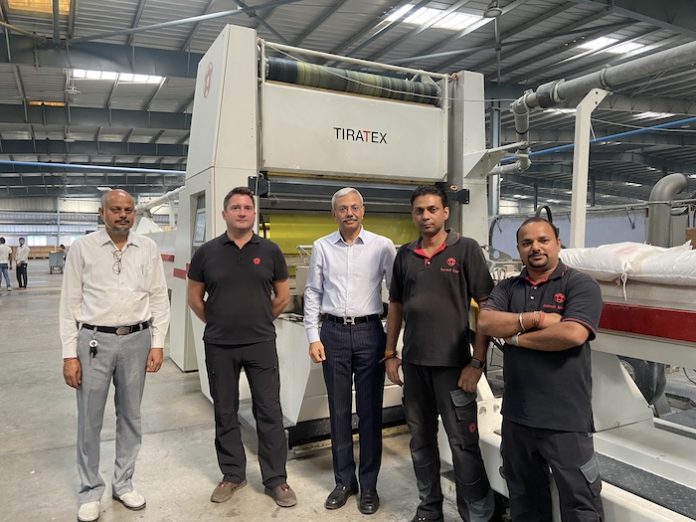
India is the second largest producer of cement globally and more than 90% of it is packed in woven sacks. Woven sacks are made of a single polymer family and are therefore already easy to recycle. However, the sustainability requirements for packaging have increased globally and at the same time, the need to develop better packaging to improve the logistics, shelf-life, and utility for commodities such as cement to reduce wastage has gained importance.
Suraj Logistix, a leading producer of polypropylene (PP) woven sacks in India, has taken several initiatives in creating more sustainable woven sacks solutions for cement packaging. The company has a strong commitment to the market it operates in and strongly believes in adhering to stringent quality parameters.
It presently has an installed annual capacity of 50,000 metric tons of woven sacks. Suraj has several W&H machines to produce high-quality woven bags. Using innovative technology on these high-quality machines, it has developed several innovative products.
Lightweight AD Protex block bottom bags for cement
The Indian market is currently using 80-82 gram block bottom woven bags. Using the W&H machine technology and the W&H sack concept AD Protex LS, Suraj has produced 74-gram bags that are already successful in the Indian supply chain. The lighter-weight bag delivers a cost advantage and makes the supply chain more efficient and sustainable.
Shri Gupta, managing director of W&H India, explains, “AD Protex block bottom bags are already a very sustainable solution, the bags are produced using hot air sealing and use no glue or threads. W&H’s Light and Strong technology is getting popular worldwide as it helps woven sacks solutions become more sustainable and cost-effective. We thank Suraj Logistix for partnering with us and investing in top-of-the-line technology. The results are excellent, and the developed products are a game changer for cement and bulk material packaging.”
Endorsing both the technology and the urgent need for sustainable solutions, Prakash Khemani director of Suraj Logistix, comments, “As a leading supplier of woven sacks, we feel responsible to make our solutions more sustainable and viable, we owe this to the industry and to the next generation. We are constantly working in this direction and the products developed are a result of extensive research and development. W&H technology certainly played a key role in our efforts. Also having a complete turnkey woven sack plant from a renowned supplier helped a lot in these endeavors. We cherish our long-term partnership and look forward to working on more such developments
Lightweight sewn woven bags
For reducing the bag weight for sewn woven bags, Suraj used W&H’s tape extrusion technology bringing down the weight of the 50-kilogram cement bags from 77 grams to 65 grams. The lightweighting of these bags has been successfully implemented in the Indian supply chain.
Bags with recycled materials
Recycling plastics for use in the supply chain for packaging materials is a critical demand to help reduce the negative environmental impacts of plastic. Suraj Logistix has developed both the AD Protex and sewn cement bags with up to 25% PIR. These bags are already in active use in the supply chain. The company also plans to increase the production capacity of recycled bags.