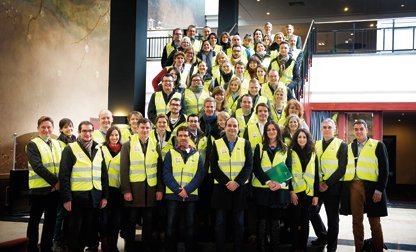
Japan has moved towards a highly efficient circular economy thanks primarily to its pioneering Law for the Promotion of Efficient Utilization of Resources, passed in 2000. The law, which treats materials as circular goods, covers the entire product life cycle. Manufacturers are required to run disassembly plants by law, with material recovery also legally mandated. Four European countries – Denmark, The Netherlands, Scotland and Sweden are also seemingly ahead of their peers. As Joanne Hunter reports, the UK has also become active in this area and amongst other measures, a Master of Science (MSc) degree course in the circular economy was recently launched by Cranfield University in the UK. The recovery of cut grass, algae and leftovers and by products of industrial processing to use in the making of new things recognizes the value and increases the worth of what is naturally occurring and man made – sound reasons for thinking in circles. The term ‘circular economy’ has become fundamentally important in the lexicon of business and industry across the UK and Europe. Without meaning…
Choose your subscription to read more
Trial
- ₹ 0 for 4 weeks*
PSA Plan 1
- ₹1,500.00 for 1 year*
PSA Plan 2
- ₹2000 for Year*
PSA Plan 3
- ₹3,600.00 for 2 year*