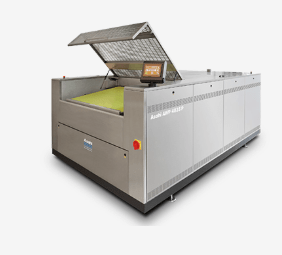
Asahi Photoproducts, a pioneer in flexographic photopolymer plate development, reported that it is participating in a project with Comexi and other industry partners. As part of this turnkey project, Asahi will place an Asahi AWP 4835 P water wash processor and Asahi AWP water-washable plates with CleanPrint at Comexi’s Manel Xifra Boada Technology Center in Girona, Spain. The project is designed to educate flexible packaging companies about the value of bringing flexo platemaking in-house and demonstrating how easy that is to do with today’s technology. “We are proud to be participating in this very important project together with our partner Comexi,” says Philip Mattelaer, Asahi Photoproducts’ head of Sales. “There is an increasing trend for flexographic printers to bring platemaking in-house, both to drive efficiency and improve quality. This project will demonstrate to the flexo market how easy it is to produce plates in-house, strengthening the value chain at the point of print production. In addition to improved efficiency and quality, this project demonstrates how print providers can drive increased sustainability by incorporating Asahi CleanPrint…
Choose your subscription to read more
Trial
- ₹ 0 for 4 weeks*
PSA Plan 1
- ₹1,500.00 for 1 year*
PSA Plan 2
- ₹2000 for Year*
PSA Plan 3
- ₹3,600.00 for 2 year*