B&R, one of the major players in the automation industry in India, will display its Industrial IoT solutions at Plastindia 2018. The Ethernet POWERLINK, openSAFETY and OPC UA solutions will enable machine builders to achieve seamless connectivity right from sensors up to the cloud.
Ninad Deshpande, B&R India’s head of marketing, spoke to Packaging South Asia correspondent Puskhar Oak about the company’s presence at the show in Gandhinagar, “B&R is a major player in the plastic industry and Plastindia acts as a great platform for us to showcase not only our products but also our solutions. At the B&R Industrial Automation stand in Plastindia 2018, visitors will witness next-generation automation solutions for building smart machines and factories together with various Industrial IoT solutions.
“Everyone is talking about Industrial IoT and Industry 4.0 readiness and at Plastindia 2018, we will show visitors cost-effective and proven solutions live in action to help them become globally competent. With open source communication networks such as Ethernet POWERLINK, openSAFETY and OPC UA, B&R enables machine builders achieve seamless connectivity throughout the chain.”
Mass customization drives automation
“The packaging industry has always led in new technology adoption. In pursuit of the smart, connected factory of the future, Industry 4.0 embraces automation, communication and manufacturing technologies – paving the way for a new industrial revolution. With the revolution will come heightened levels of networking and integration between companies in value networks. This type of collaborative partnership relies on interoperability, transparency and decentralized intelligence to ensure operational consistency throughout a multi-vendor environment. Maximum productivity and extensive product customization under mass production conditions are the central goals of Industry 4.0.
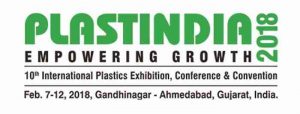
The new I/O modules measure the temperature and humidity in the control cabinet and log much time the values spend within defined ranges
“Mass production is something of the past and machine builders are looking at mass customization. Today, manufacturing units look at achieving economical production even at a batch size of 1. The focus is on having adaptive and flexible manufacturing coupled with higher overall equipment effectiveness (OEE), data acquisition and analytics. Reducing downtimes too is a prime concern for packaging and plastics industry. Maintenance is looking at moving from reactive, preventive to predictive maintenance. Industry 4.0 and the Industrial Internet of Things (IIoT) promise to reduce total cost of ownership by making machinery easier to operate and maintain. Mass customization requires highly modular machines to enable automatic adaptation of production to real-time demand.
“Widespread adoption of PackML and OPC UA ensures operational consistency between all the machines in a multi-vendor packaging line – for a substantial boost in overall equipment effectiveness. Integrated condition monitoring and direct web connectivity down to the sensor level will serve big data analytics and enable auto-diagnostics. Complemented by augmented reality technology, access to comprehensive diagnostics via standard web technology enables total productive maintenance. The result is improved production with zero defects, zero breakdowns and zero accidents.”
B&R’s ACOPOSTrack
“B&R provides machine and factory automation solutions for catering to various demands of the plastics and packaging industry, and is an ideal partner for a successful Industrial IoT implementation. In 2018, the company is redefining the production economics and equipment effectiveness with ACOPOSTrak. Its unique design enables machine builders to capture the benefit of small batch flexibility.

temperature and humidity in the
control cabinet and log much time
the values spend within defined
ranges
“ACOPOStrak is a revolution in adaptive manufacturing that extends the economy of mass production down to batches of one. Parts and products are transported quickly and flexibly from processing station to processing station on independently controlled shuttles. It is a generational leap in intelligent, flexible transport systems. Its design delivers decisive technological advantages for adaptive, connected manufacturing. It helps machine builders to produce small batches efficiently and benefit from the higher margins of personalized products and extends their digital transformation to include motion control and mechanical design. ACOPOStrak boosts your overall equipment effectiveness (OEE), multiplies your return on investment (ROI) and accelerates your time to market (TTM).
“In addition, B&R has introduced the world’s first image processing solution to be seamlessly incorporated in the automation system making machine vision an integral element of the automation ecosystem. The solution comprises cameras, software and lighting accessories. At the heart of the solution is a broad selection of intelligent camera technology. Options at the lower end will replace simple machine vision sensors, while the top of the range will harness the full potential of high-end smart cameras. Ready-made software components are available for creating applications with minimal new programming.
“On 6 July 2017, B&R became a business unit of the ABB Group. As a global leader in industrial automation, B&R combines state-of-the-art technology with advanced engineering to provide customers in virtually every industry with complete solutions for machine and factory automation, motion control, HMI and integrated safety technology. Our visitors at Plastindia 2018, will be able to witness how B&R is constantly redefining the future of automation engineering.”
On plastic processing machinery
“Plastic processing machinery needs to be more flexible and more efficient than ever. With these requirements increasingly being solved in software, software engineering is consuming a rapidly growing share of the development budget and schedule. Mapp Technology makes software development much easier and faster and we move from programming to configuration. The unprecedented levels of machine-to-machine and plant-wide networking that distinguish IoT and Industry 4.0 solutions can only be achieved with uniform communication standards.
“The plastics industry was quick to recognize and implement this requirement with the EUROMAP recommendations. B&R has incorporated these interfaces directly into its products in the form of precoded blocks that offer OEMs ultimate convenience during development. At Plastindia 2018, visitors will learn about these standards and the ease of implementation with B&R systems.
“Servo hydraulics plays an essential role in plastics processing machinery. Automatic tuning processes help get the most out of every system – for machines that are fast to set up and efficient to operate. Visitors will learn about our offering on the integrated functions for optimizing servo-hydraulic systems,” shared Deshpande.
Plan 2018
Talking about B&R’s plans for this year, he said, “Modern production processes generate enormous volumes of data that can provide valuable feedback about equipment utilization, productivity and energy efficiency. With this real-time data, there is huge potential for continuously optimized operation. We will be highlighting our solutions for factory automation comprising of PDA, energy monitoring and condition monitoring.”
Smart-factory intelligence with Orange Box
“We help machine builders become ready for Industrial IoT by enabling them to achieve plant-wide data exchange, remote data access, analysis of data from heterogeneous sources, integration of different field-bus technologies and digitalization of manufacturing systems. Edge computing hardware from B&R ensures that the machine data gets from its source to the cloud safely and securely. At Plastindia, we invite machine builders and their customers to discover B&R’s edge solutions and the many pre-processing options they offer.

system ACOPOStrak
“B&R’s edge solutions send aggregated, pre-processed data to the cloud. The cloud handles any remaining computational tasks as well as providing long-term archiving. Implement long-term evaluation and forecasting – Industrial IoT becomes reality. As far as brownfield is concerned, B&R make advanced analytics for brownfield assets easier than ever with a cost effective solution. B&R’s Orange Box lets users access previously unreadable energy and process data from digitally isolated machinery. The Orange Box is able to read data from the machine without any changes to existing hardware or software. Clearly visualized performance metrics make it easy to identify opportunities for targeted improvement so machinery can be operated more efficiently. As an Industrial IoT solution package, the Orange Box brings smart-factory intelligence to brownfield installations. To witness Orange Box, live in action, please do visit the B&R stall at Plastindia 2018.”