
“We are looking at complete in-house packaging to improve our quality as well as brand presence. It is in line with our strategy of backward integration and expansion,” says BP Agarwal, chairman, Surya Fresh Foods, which produces 600 tonnes of biscuits, cookies and chocolates each day.
Surya Fresh Foods owners of the Priyagold biscuit brand has installed a ‘dream machine’ – a Rapida 105 6-color plus coater full UV press at its new carton plant at Surajpur in Greater Noida. The Rapida 105 at Surya has three interdeck and one end of-press UV curing systems and is capable of printing 16,000 sheets an hour. The sheets are converted to monocartons for biscuits by a Bobst Novacut 106 diecutter and the Bobst Lila 106 A2 folder-gluer. Litho-laminated microflute cartons are produced using a Chinese sheet laminator from Boagang Machinery. A separate area houses the corrugation plant for secondary packaging.
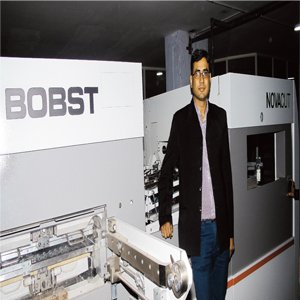
The in-house printing and packaging set up removes all critical issues of quality, timely delivery, operational flexibility and security. The 6-color UV KBA Rapida 105 is used by Surya to print CMYK and two special colors for their biscuit packs. “One of the special colors is our base color which could be blue, brown or orange and the other we use for our logo,” says Dinesh Prasad, plant manager. In addition to the Bobst Novacut 106 for diecutting, the Bobst Lila 106 A2 folder-gluer can produce both straight line and crash lock bottom boxes.
“We may require one more diecutter when the 105 KBA runs at full speed and at full capacity. Currently our monthly requirement is about 12 to 15 lakh sheets, which we can easily produce by running the KBA for a single shift and the diecutter in two shifts if necessary in situations of peak demand,” says Dinesh Prasad, plant manager, Packaging Division at Surya Fresh Foods. “We produce boxes of 6 to 7 sizes as per our requirements,” Prasad adds, “and the lack of consistency in quality was a major pain area. This led us to set up this in-house packaging unit.”
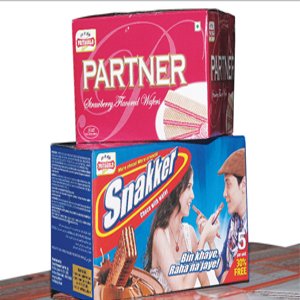
boxes in 6 to 7 sizes. Photo PSA
The greatest advantage of having an in-house packaging unitis that control andflexibility canbegainedatdifferentlevels of production. For the Priyagold biscuit cartons, the lead
time has come down drastically and the production has become more organized. “Earlier, when there was a shortage of packaging material, ittook us around 10 days to getthe material shipped from the supplier. However, now we are capable of forecasting demand three days in advance and deliver the cartons to our biscuit manufacturing plants just-in-time. We also have the choice to pick and process jobs on the basis of priority,” says Prasad. “With the KBA 105 6-color plus coater UVpress,the color quality and consistency ofthe cartons has improved manifold and so has the brand visibility. The new press gives us the flexibility to maintain our brand logos and other crucial elements while adding special embellishments and special colors when needed without the lead times and hassles faced by us when we outsourced our packaging.”
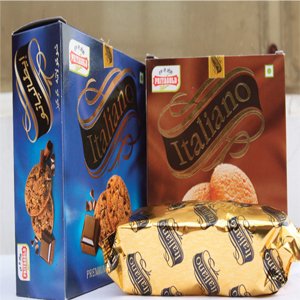
Photo PSA
Surya started its business in November 1992 and launched itsPriyagold biscuit brand in October 1993. Over a period,the companymanagedto establishstrongbiscuitmanufacturing
capabilities and invested substantially in developing consumer preference for its products. Its brands ‘Haq Se Maango’ and ‘Priyagold’ emerged as powerful brands in the FMCG sector.Today,the companyhas threeplants locatedinGreater Noida, Lucknow and Surat and has diversified to upmarket biscuits and chocolates as well.
According to BPAgarwal, chairman Surya Fresh Foods, the company produces 600 tonnes biscuits, cookies, chocolates and cakes daily. Agarwal who believes in changing his market strategy according to customer demand and seasonal and other preferences, says, “In today’s market, it is very crucial to have consistency in printing quality or the brand will fail. For that, you need a well-equipped and standardized in-house printing and converting facility so that you can take control of everything that can help your brand achieve maximum touch points on the shelf.”