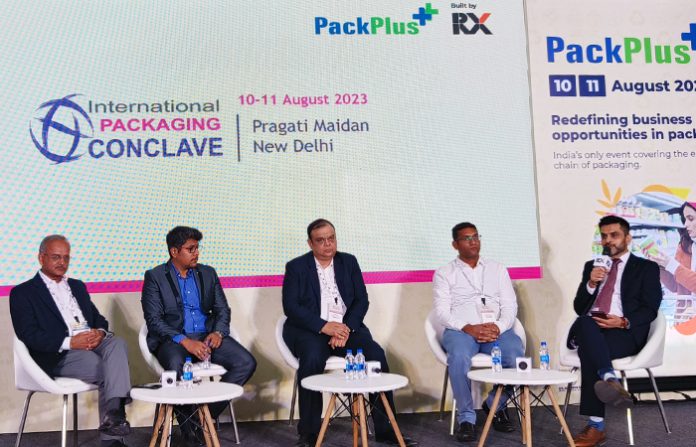
A session on ‘Enabling Manufacturing Freedom with Adaptive Technology’ was held as a part of the PackPlus International Packaging Conclave, on 10 August in New Delhi’s Pragati Maidan. Ashish Rathi, associate director, KPMG was the moderator for the panel.
Digital advancements such as robots, IIOT and AI have taken the packaging industry by storm, Rathi shared, adding it will be interesting to see how these technologies will be relevant to the manufacturing processes in packaging organizations, he said.
Rahul Verma, manager – business development – North region, B&R industrial automation said, “We are partnering with our end users and machine builders for building sustainable solutions. These days, the consumer buying patterns are changing very fast and to adapt to that, we are coming up with a lot of adaptive machines.”
The Covid-19 pandemic launched an era where we are more focused on packaging. We are now producing products where we do not want any human hand touching the products, said Vipul Gupta, senior manager e-factory sales, Mitsubishi Electric India. “We want to improve the adaptive packaging for the Indian landscape.”
Bharnidharan Sekar, chief manager – software, at Addverb talked about how automation can enable the factories of the future to aid in this age of instant commerce.
B&R’s Verma shared about robotics and AI in automation, “If we talk about the manufacturing sector, there are new types of challenges which were not there earlier. The first of these challenges is the product life cycle. There is demand fluctuation along with seasonality – this leads to the need for mass customization of products. Consumers, these days, also have good purchasing power, which was not there earlier. They want a product that is specially created for them.
“We are moving from mass production to mass customization. Robotics and AI should come together to solve these challenges. Robotics is mostly used in discreet operations and end-of-line solutions. Going forward, robots will be an integral part of the machine. Robots, machine systems, intelligent transport systems and digital twin tools to visualize them in real-time are the four pillars of adaptive machinery. This entire system should have intelligence,” Verma said.
Sekar said that the packaging lines today should be intelligent enough to know the incoming product and in a way adapt itself so that what could have been a potential bug earlier can be a new product for the customer now. “We are talking about food packaging lines that detect the recipe of the products on the fly, and, accordingly, print the content of the label on the fly. Guided vehicles or autonomous mobile robots are today a part of the fleet to aid the operator to smartly convey the raw material.”
Most of the adaptive automation that is being done today is for end-of-line operations, Naresh Kantoor, managing director, Encon Systems, said. “The first challenge is that of space. The warehouses in India, at the moment, are not designed keeping in mind complex automation. The second challenge is investment – these adaptive flexible systems have a huge cost attached to them. The management is not mentally prepared to justify this kind of investment for the benefit they are going to derive today. The third challenge is integration with the parent machine, which has its own characteristics, and SKUs. The last challenge changes in the network because everyone is used to contract labor in the network.”
Emerging technologies come from the present challenges. Right now, the emerging technologies are moving toward how to solve the challenge of mass customization, Verma said. “How we can know the defects in advance, and how we can correlate them using AI. In India, we are already doing a lot of innovations that require a lot of investment – if a person is making investments, he gets the advantage of being the prime mover in the market. If we have to move along with the future trends such as mass customization, we have to remove the defects, and provide zero changeover downtime.”
Sekar spoke about ESG in automation, “One of the key points in packaging is the effluents that get generated. When you have automation, the amount of reuse or recycling that you are going to have with the effluents will be significantly high. In terms of social, we are raising the basic capabilities of a person, who might not have understood Microsoft Excel earlier but has the proficiency to use smart tablets today. Governance is all about audit-ability, traceability, and having a piece of data that we can go back in time and look at. When you have technologies such as print and apply machines, checkweighers, quality functions are not control-oriented, rather they are assurance oriented.”
Data handling on a real-time basis is the first thing you need to deal with while creating an automated factory, Gupta said. “All stakeholders can monitor the data at the same time and respond to the need for the change required. This brings more flexibility in the system, more consistency in the product, and more quality orientation that will lead to all stakeholders becoming more responsible. We have implemented data-edge computing in our factory also, which has led to decision-making at the plant level.”