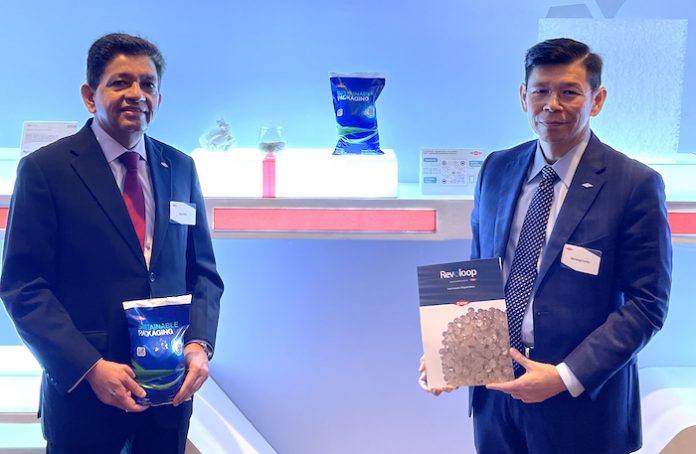
On a sunny New Delhi morning, across the city from the PlastIndia exhibition taking place in Pragati Maidan, we met with Dow’s commercial vice president of Packaging and Specialty Plastics for Asia Pacific Bambang Candra along with Vipul Babu, the company’s sales director for Packaging and Specialty Plastics Business in the India Subcontinent. The meeting and conversation took place parallel to PlastIndia at an off-site location where Dow organized its display of materials, samples, and brochures for film converters, technologies, and brand owners. A comfortable and peaceful way of showing and explaining its latest developments enabling circular packaging.
As Candra explained to us, Dow is fully aware of the climate change issues surrounding plastic-based packaging. “We are aware of the issue,” he said, “and Dow as a material science company has the vision for this industry to be successful and green in the future. With our technology, we believe that with material science technology we can make this plastic circularity happen. For us to do that we start from the beginning – by designing for circularity. It was a challenge, in the beginning, to decide what the needed functionalities were. Keep in mind, that for us plastic is still the best material for capturing carbon or keeping the lowest carbon footprint.”
Explaining the advantages of PE monomaterial packaging, Candra said, “There are several ways of recycling and one of the ways is mechanical recycling – for us to have this mechanical recycling we would like to have this monomaterial in the packaging where will be providing the functionality with our technology. Using PE we can prove several applications and you can see some of the samples that we are showing.
“To put this in the specific context for India, let me say that when this idea came out about five years ago, India was among the first, at least in my territory, to adopt this idea whether it was for rice packaging or Tata Salt. This was when nobody believed it could happen but it was a good start. Now, when the Indian government is also putting specific targets about extended producer responsibility (EPR) and with PCR use by 2025, we believe this is going to accelerate the adoption of the technology.”
Babu explained that while Dow is looking at all the ways of making films, over the past five years, it has been able to provide resins for conventional blown film lines to produce PE films that are printed on existing gravure presses. “You can print these films on the gravure presses at the same speed as polyester films. This can be done by a converter in-house today and it is as competitive as a polyester laminate for some applications.”
Candra added that Dow is looking at the entire packaging development and supply chain in India and not merely the supply of its new PCR materials such as Reveloop that were ubiquitous at the stands of several blown film manufacturers’ stands at K22 in Dusseldorf last October. Looking at full circularity means that Dow has taken an interest in the burgeoning Indian plastic waste collection and recycling industry directly by collaborating with recyclers such as Lucro Plastecycle, and indirectly as a founder stakeholder of Circulate Capital which in turn has invested in several Indian recycling companies.
PE-based recyclates gaining traction
Candra and Babu say that both compliances with plastic waste collection and recycling as well as the use of inputs such as Dow’s Revoloop are gaining traction in the country. In fact, some Indian flexible film and packaging converters are asking Dow to ramp up the supply of these Post Consumer Recycled resins. To make these, the used plastics are cleaned, shredded, and reground to create new plastic pellets and mixed with virgin resin to create new resin inputs.
60% PCR single pellet PE resin
Candra says it is possible now to supply a Revoloop resin that incorporates 60% post-consumer recycled polyethylene. Looking at the challenges of using these inputs to produce films with consistent quality and consistency, Dow is offering Revoloop as a single-pellet solution, which improves the accuracy of the dosing of the blown film lines. The Revoloop pellets enclosed in its brochures are quite clear and odor-free as are the enclosed 50-micron film samples made from it.
The recommended applications for these PCR resins include detergent pouches, shampoo sachets, and various liners and courier bags. For food packaging, there is still some way to go before recycled materials are approved by regulators and both Candra and Babu suggested that for this level of circularity to reach fruition – a higher order of recycling such as chemical recycling may be needed – which they also described as “advanced recycling.” Notably, Candra said, “We are looking at all the technologies, and in chemical recycling too, where technology inputs are needed, we are engaging with Indian companies.”
Although the discussion was wide-ranging among the most interesting points was that Dow has established a packaging design and testing center in Navi Mumbai that is available for converters to experiment or produce prototype films with its resins. The center has both a lab-sized blown film line as well as a Flexotechnica laminator for pilot production and testing of new films and laminates.